I have often found that when people talk LEAN they tend to focus on lean manufacturing, which has created the perception that lean principles can only be applied to a manufacturing environment. This is far from the truth. In fact, one of the underlying principles – a few more will be discussed later in this article – is that of improving the whole (end-to-end supply chain). There are varying views on the origins of lean and is known by a variety of names such as Toyota Production System (TPS), lean production and lean manufacturing.
One of the definitions of lean is: “A systematic approach to identifying and eliminating waste through continuous improvement, flowing the product at the pull of the customer in pursuit of perfection.”
Whilst it can be applied to specific areas within an organization, it encourages the use of principles and tools that are meant to optimise the entire supply chain. The lean approach results in a continuous improvement culture that is evident throughout the organisation. Cross functional teams look to drive improvement projects that promote system wide improvements over functional (silo) benefits. The below diagram illustrates a typical supply chain:
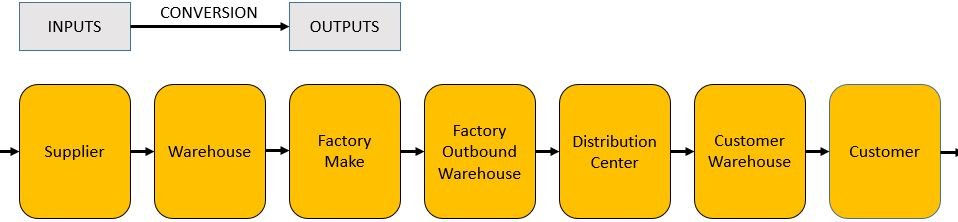
1. Some Lean Principles
Whilst these principles are sometimes considered to have the highest impact within a manufacturing environment, I will specifically use examples to illustrate how they are relevant to the entire supply chain. The below equation reflects what makes up a supply chain:
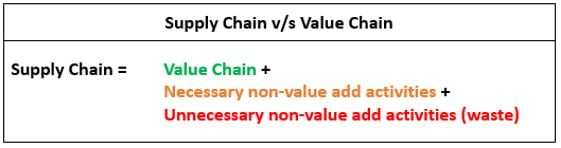
The aim is to show that a supply chain has the following high-level components:
- Value chain
These are all activities that contribute towards the final product or service that your customer is willing to pay for. They perceive it to be good value for the amount that they are paying to purchase the product.
- Necessary non-value add activities
There are countless different activities within a business and not all add value. In fact, customers would rather not pay for non-value activities. However, understand that it is a necessary evil. The cost of transport from the warehouse to the store does not increase the perceived value that the customer gains but they realise that is the only way they can get the product. Whilst they may not be happy about it, they realise the cost is built into the product. The trick is to minimise these costs and therefore reduce the cost of the product.
- Unnecessary non-value add activities
You are probably wondering why anyone would want to perform any activity that adds no value. Imagine your warehouse operations consistently results in stock being damaged by the forklift and being dumped. From a product costing perspective the organisation has to recover the money so they build these as an allowance to recover the expense of the wastage. As customers, we definitely are not happy about paying for this. The trick is to reduce or eliminate these unnecessary activities.
1.1 Eliminate waste
Waste elimination is one of the more common principles which receives a fair bit of attention. Often, we consider and focus on production related waste though there are at least seven other wastes that lean describes (see below). Over forecasting customer demand results in more products being manufactured and warehoused also has the potential of that stock expiring before it could sell. This is an example of waste, but the root cause does not sit in production or the warehouse – it actually sits within customer demand forecasting.
1.2 Build quality in
I am sure you often hear people talk about ISO and SABS quality standards. It is the ability of an organisation to implement quality management systems that focusses on both quality assurance and quality control. The approach looks at ways to ensure quality outputs throughout the chain.
1.3 Create knowledge
An often forgotten aspect of lean – if an organisation culture of teamwork and continuous improvement is promoted, employees continuously seek innovative and creative ways of solving problems. The result is the organisation creates their own body of knowledge which is widely shared and used. No one wants to reinvent the wheel.
1.4 Deliver fast
As an organization, how do you minimise lead times to ensure you can deliver as quickly as possible? The premise is that if you can minimise lead times, you do not have to hold additional inventory of finished goods, work in progress or materials, which in turn reduces costs.
1.5 Optimize the whole
As mentioned previously, the focus is always on the whole. Any action, activity or project must yield organization-wide benefits. Teams are actively encouraged to evaluate project benefits holistically. In 1.1, we used the example of the root cause of stock expiring originating in the forecasting arena. Understanding the value stream maps and having the mindset do what is right for the business versus departments breaks down silo’s and results in optimisation of the whole.
2. The Seven Wastes described in lean
One of the pillars of lean is that you must have the mindset to drive out waste. The typical wastes discussed are:
2.1 Defects
Defects are probably the one that we are the most familiar with. In a manufacturing plant, quality control checks which identify products that does not meet the standard are then reworked or discarded – which comes at a cost. However, if the same product is not identified and makes its way to the shelf and a consumer buys it, returns it and complains, the cost is substantially higher. It is a loss in terms of time, money, resources and customer satisfaction/brand reputation.
2.2 Overproduction
When we produce to stock, which is typical in a ‘push’ type supply chain, it could result in the organisation carrying excessive stock which is not required. This results in high working capital and attracts other costs such as additional storage costs, insurance, risk of expiry and damage, etc.
2.3 Waiting
If a task is waiting on an upstream task/activity this is wasteful use of resources. Imagine a refrigerated truck arrives at a warehouse to pick up a customer order of ice cream, but the warehouse has not picked the stock and made it ready for dispatch. Therefore, the truck has to wait with the refrigeration unit running to maintain the temperature of the vehicle. During this time the business incurs costs as the truck (asset) is not being fully utilised.
2.4 Inventory
Inventory is also linked to overproduction. It is when we carry more stock than we need. Note this does not only apply to finished goods but to all forms of inventory (raw materials, packaging materials, engineering spares, work in progress, etc).
2.5 Transportation
Let me say that most transportation is wasteful but as explained above, it is necessary. The aim is to minimise transportation and movement of resources (material & product) as this will cost you in time and money, resulting in lower outputs. Example: Transporting goods on a truck that is 60% versus 100% utilised between two cities is wasteful. Improving the average utilization will result in fewer trips being required.
2.6 Motion
Most organisations will state that people are a critical asset. If so, then we should be ensuring that we eliminate the unnecessary movement of people as this results in lower output per employee. Example: An employee walking between two workstations to fetch a component each time versus equipping the employee with a trolley so that he can fetch five units at a time.
2.7 Excess Processing
When we do more work on a product that what the customer wants, it is considered excess processing and is a sign of a poorly designed process (also known as over-engineering).
Conclusion
Lean principles and tools are a wide topic with no shortage of material. The above article looks to explain some of it in context of the broader supply chain. I especially wanted to highlight that you should not focus on functional departments (silo’s). If you are serious about implementing lean, you must create a culture and mindset that looks at the entire supply chain. Apply the tools to determine root cause. There can be no ‘holy cows’ or areas that are seen as untouchable.
Author
Dr Kenneth Moodley is an experienced supply chain and business professional with over 25 years’ experience. He has a demonstrated history of working with both big corporates (example: Unilever & The South African Breweries) and SMME’s (Productivity SA) in various industry sectors as a senior Supply Chain Specialist, Leader and Business Coach. In addition to his supply chain experience, he is a skilled business turnaround strategist and is a registered senior business rescue practitioner.
Join the discussion One Comment